Rogue Components: Their Effect and Control using Logical Analysis of Data
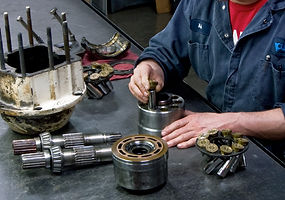
There is a small subset of any repairable component population that can develop a failure mode outside the scope of the standard repair and overhaul procedures, which makes them “rogue”. When this happens, a Darwinian-like “natural selection” phenomenon ensures that they will be placed in the most disadvantageous position in the asset management program, negatively affecting multiple aspects of the operational and maintenance organizations. Rogue components have long plagued the airline industry and created havoc in their asset management programs. In this paper, we describe how these rogues develop, outline the natural selection process that leads to their hampering the asset management program, and examine some of the negative impacts that ensue. Then we propose a Condition Based Maintenance approach to control the development of these components. We explore the use of a supervised learning data mining technique called Logical Analysis of Data (LAD) in CBM for the purpose of detecting rogues within a population of repairable components. We apply the resulting LAD based decision model on an inventory of turbo compressors belonging to an airline fleet. Finally, we evaluate the applicability of LAD to the rogue component detection problem and review its efficiency as a decision model for this type of problem.
Case Studies
Optimizing the performance of railway service by using data mining and advanced artificial intelligence techniques

We are looking for improving the performance of railway service through predicting failure conditions and equipment degradation behaviors. We use an approach that can identify and characterize failure conditions and equipment degradation. This guides the maintenance department in scheduling maintenance operations based on the conditions of the equipment. Moreover, we evaluate the usefulness of the available databases collected by means of existing sensors, inspection devices, and other monitoring processes. This evaluation identifies the factors that play an important role in monitoring equipment conditions and predicting failure, and other factors that are not useful in anyway. cbmLAD is applied to extract knowledge form the measurements records. LAD, as a data mining approach, is capable of identifying conditions of failure and of determining which measurement can indicate that failure or degradation is happening, and which can be considered redundant. Moreover, cbmLAD provides a classification tool that can be used to diagnose the conditions of the equipment as good or critical. The knowledge extracted is represented by sets of interpreted and meaningful patterns, where each pattern refers to critical or normal status of the equipment under study. These patterns are obtained by solving a pattern generation problem. The pattern generation problem is the building block problem in implementing LAD technique to large scale applications.
Machining process monitoring by using machine learning and advanced artificial intelligence techniques
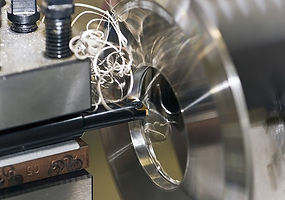
A key issue for unattended and automated machining operations is the development of reliable and robust monitoring systems. These systems should be capable of detecting the tool deviations in order to prevent the tools, the workpieces and the machine’s damages during the machining of difficult to cut materials such as Titanium, Waspaloy, Nickel based powder alloys, under different machining operations. Since sensors’ and information technologies are both expanding rapidly and continuously, it is expected that data analytics techniques will help in blazing a new trail in monitoring machining processes by using state of the art techniques in order to significantly reduce the cost of machining process and prevent the tools, workpieces and machine damages during the machining. Research in machine- learning and artificial intelligence offers some new techniques that do not depend on statistical assumptions and that offer clear, unambiguous and transparent solutions to the unsolved problems of machining processes.
Our objective is to improve the monitoring of machining processes in order to reduce cost and prevent the tools, workpieces and machine damages during the machining. In order to achieve this improvement, data mining and advanced artificial intelligence technique called Logical Analysis of Data (LAD) is used. LAD has the ability to identify the tool conditions and to determine which machining conditions can indicate that the tool failure or degradation is happening, and which conditions can be considered redundant. Moreover, LAD provides a classification tool that can be used to diagnose and map the machining conditions in order to identify which parameter affects the quality and geometric profile of the machined part. A robust machining monitoring system especially for critical rotating parts will keep the quality of the process under control and highlight any deviations in closed-door process.
Using Artificial Intelligence to Optimize the Pavement management of Routes

We seek to adequately discriminate the state of pavements of routes. We simulate the deterioration of the road network by using artificial intelligence techniques in order to establish the network status, the need for action and the budgets required when simulations of different investment scenarios are adopted.
Our goal is to define profiles or homogeneous characteristics of segments of roads using artificial intelligence. The obtained profiles allow better understanding of segments’ deterioration upon aging and use.
Fault Diagnosis in Industrial Chemical Processes using Interpretable Patterns based on Logical Analysis of Data
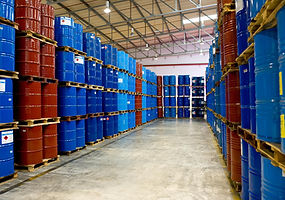
In critical chemical processes, the incipient faults may cause abnormal operations or emergency shutdown, and even plant damage or casualties, if they are not detected and diagnosed early enough. To achieve safe and optimal operations in such processes, advanced fault detection and diagnosis schemes are used. The existence of efficient diagnostic schemes minimizes the quality and productivity offsets, and avoid the risk of hazardous consequences in abnormal operations. Our objective is to build an efficient diagnostic routine based on the data collected from the controlled process. The software cbmLAD is used in order to extract knowledge from a huge amount of data and to transform them into comprehensive knowledge-base. This knowledge is then used to perform an inference for decision making.
Fault Diagnosis and Prognosis of the performance of a biomass recovery boiler in pulp and paper industry

The recovery boiler is at the heart of the recovery process. In this process, the wood is dissolved using the pulping chemicals (NaOH and Na2S), resulting in black liquor that is separated from the pulp by washing. The black liquor is then sent to the recovery system in order to recover the inorganic chemical for reuse. The dissolved organics are used to produce steam and power. On average, over 1.3 billion tons per year of black liquor are processed and burned in the recovery boiler in order to produce 700 million tons of high pressure steam. The black liquor is the fifth most important fuel in the world, coming after coal, oil, natural gas, and gasoline. Fault diagnosis in biomass recovery boiler is challenging, due to the large number of manipulated and measured variables, and due to the interactions of the sub-units in such complex system. The discovery of interpretable patterns is used in order to build a decision model (classification rule) that classifies sensors observations, and to analyze these observation using machine learning techniques in order to detect any fault as it happens.The software cbmLAD is used to discover the knowledge in partial recovery boiler’s data which is a critical and complex part in the pulp and paper industry. The extracted patterns are found to be useful for the boiler’s operator wherein he or she can detect any fault and relates it to the causes that contribute to its occurrence, and can also update his or her knowledge.
Performance optimization of drilling and blasting operations in open-pit steel mining

Mining operations are subject to hazards and risks normally associated with the exploration, development and production of natural resources, any of which could result in production shortfalls or damage to persons or property. In particular, hazards associated with open-pit mining operations include, among others:
• Flooding of the open pit;
• Collapse of the open-pit wall;
• Accidents associated with the operation of large open-pit mining and rock transportation equipment;
• Accidents associated with the preparation and ignition of large-scale open-pit blasting operations;
• Production disruptions due to weather; and
• Hazards associated with the disposal of mineralized waste water, such as groundwater and waterway contamination.
We apply a risk identification and estimation process based on machine learning technique, namely the Logical Analysis of Data (LAD). LAD is an optimization combinatorial data mining algorithm based on Boolean logic, LAD. It generates patterns which are interactions of hazards- related causes that characterize and distinguish the events of accidents. The objective is to generate patterns which recognize and characterize classes of hazards events. The software cbmLAD is used to exploit the historical data and to generate meaningful patterns. The quantitative information given by cbmLAD about the patterns generated can be used as a logical way to identify and prioritize risk factors and potential hazard causes. This enables safety practitioners to make decisions regarding safety measures.
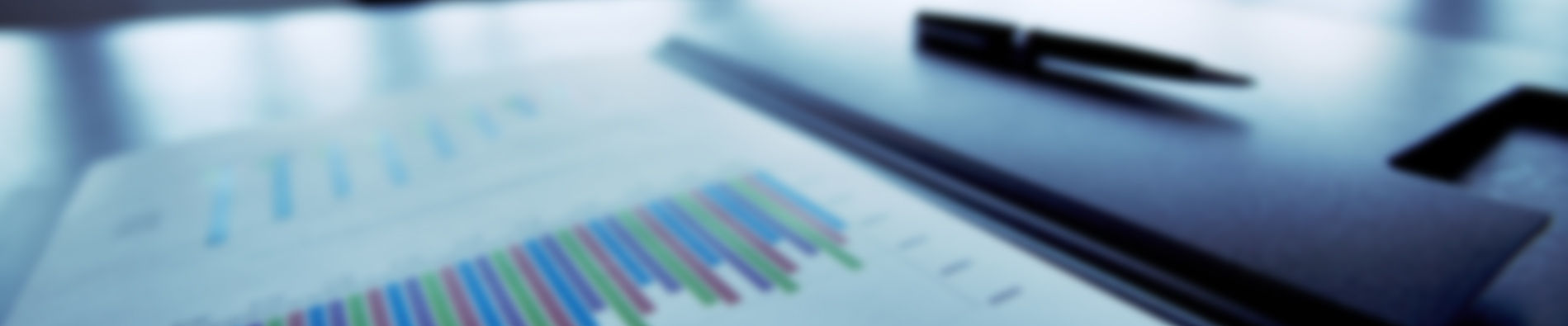